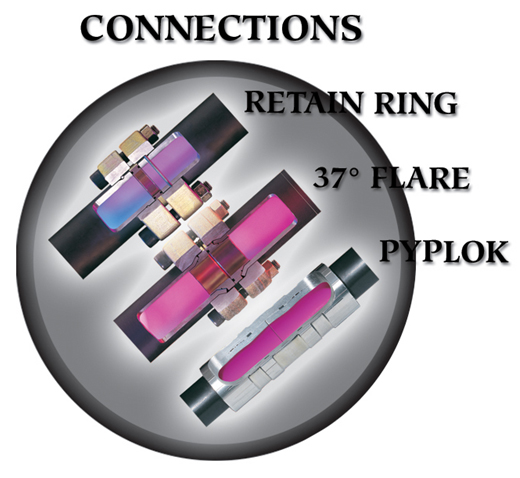
After cutting and preparing the pipe…
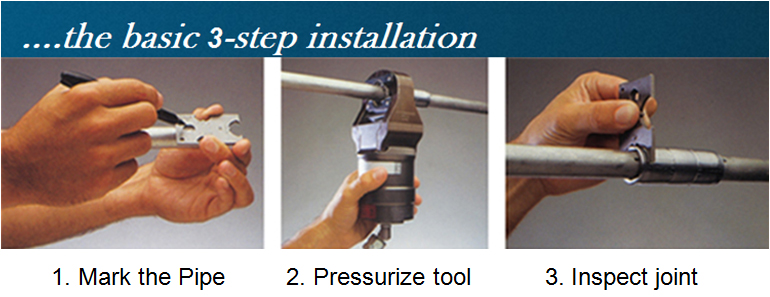
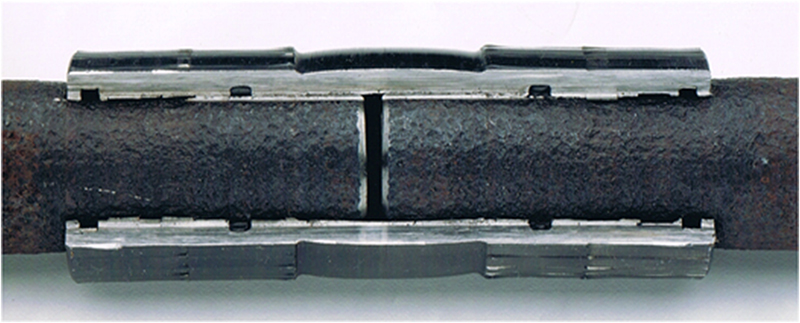
- Sample above : ¾” NPS pipe pitted due to years of exposure
- Performed 6,000 PSI (420 bar) hydrostatic proof test
- 1,000 Psi (70 bar) nitrogen leak test
- Zero leakage detected
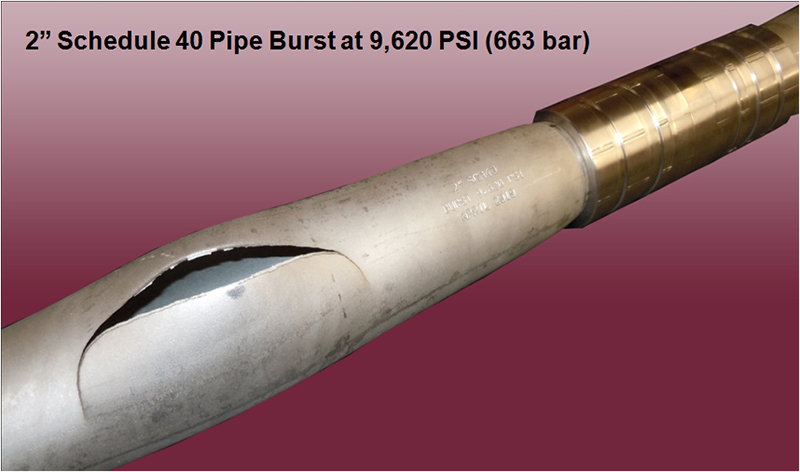
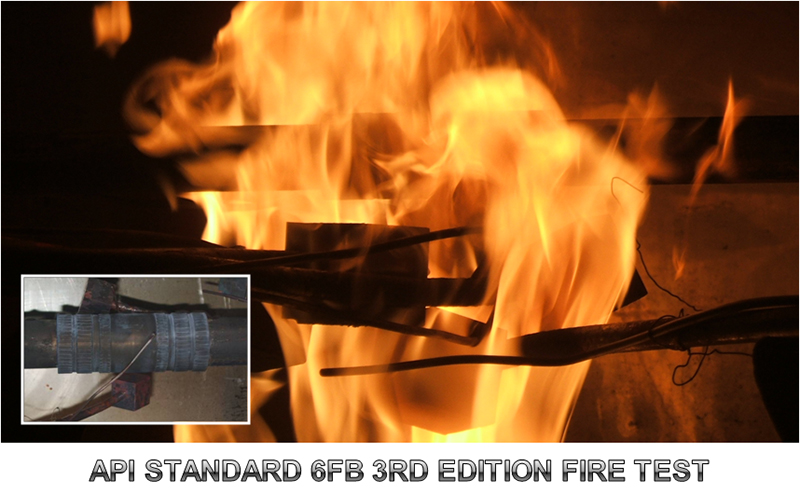
TEST | REQUIREMENTS | RESULTS |
Gas Leak Test | Gn2 Nitrogen 1,000 PSI for 10 minutes | No leakage |
Hydrostatic Burst | Based on 4 x Operating Pressure held for 5 minutes | No leakage |
Hydrostatic Proof | Based on 1.5 x Operating Pressure held for 5 minutes | No leakage |
Vibration Test | 20,000,000 cycles at displacement @ operating pressure | Passed |
Impulse Test | 500,000 cycles @ 1.33 x Operating Pressure based on ISO/BS Impulse Cycle | Passed |
Impulse/Flexure and Fatigue at Low Temperature | Simultaneous impulse and bending stress, 8 times during test of 10,000 cycles each under peak pressure and rated bending each fitting was subjected to -100 deg F for one hour utilizing liquid CO2. | No leakage |
Tensile Test | Fitting was installed in tensile machine with cross head speed of 0.20 in/min and pulled until one side of pipe dismembered from the fitting/pipe joint | Exceeded Tensile Strength by a factor of 1.33 to 1.63 |
Torsion Test | At various Torsion Angles and Ft-Lbs of Torque @4500 Psig (Gn2) and 6000 Psig (Hydraulic Fluid) | No Leakage |
Heat Aging | Maintained at 400 deg F ± 5 deg F for 168 hours, Proof test @ 6000 Psig for 30 minutes | Passed |
PYPLOK Approvals and standards
- ISO 9001:2008 Certified
- ANSI/ASME B31.1 and B31.3
- ANSI/ASME B31.4
- ANSI/ASME B31.8
- CRN - Canadian Registration No. 0A12153.5
- TSSA – Technical Standards and Safety Authority
- ABSA – Alberta Boilers Safety Association
- API 6FB Third Edition Fire Test for end connection fittings
- ISO 19921 Fire Test, Fire Resistance of Metallic Pipe Components with Resilient and Elastomeric Seals
- NAVSEA - United States Naval Sea Systems Command
- US Military Navy Shock Test MIL-S-901D
- ANZAC - Australian, New Zealand Navy
- US Coast Guard
- Canadian Coast Guard
- ABS - American Bureau of Shipping, Certificate 02-HS269945D/2-PDA
- DNV - Det Norske Veritas, Certificate P-13306
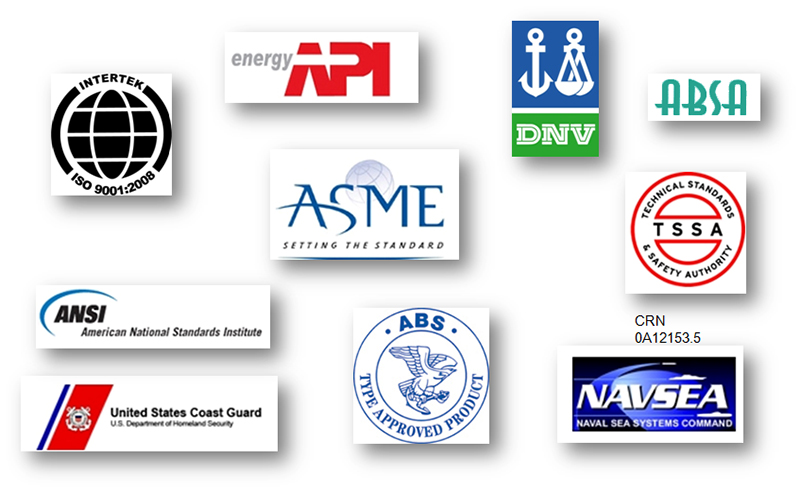
Tube-mac successfully achieved type approvals from IACS (International association of classification societies) Members…
- LR – Lloyds Registry
- DNV – Det Norske Veritas
- ABS – American Bureau of Shipping
- CCS – China Classification Socie
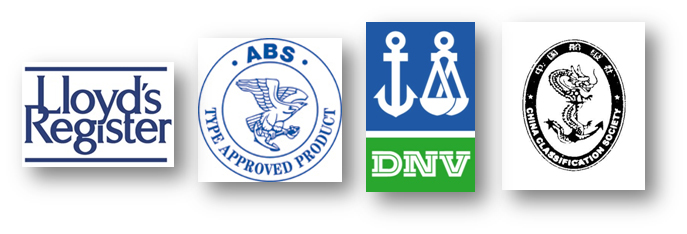
- No special skilled labour required vs. qualified welder.
- Actual swaging time is measured in “seconds” vs. “hours” for a welded joint.
- No special hot work permits
- No fire watch personnel required.
- No leaks as a result of stress fatigue cracks as seen in welds.
- No off loading or purging of fluids and gases.
- No cost to x-ray welds.
- No cost to re-work welds.
- No acid flush chemicals and neutralizers required.
- No added cost or environmental issues to dispose of chemical waste.
- SAFE cold work fitting technology.
- SAFE and easy to install in tight confined places.
- SAFE permanent, tamper proof connection.
- One piece fitting versus multi-piece bite-type fitting.
- No threads or nuts that loosen over time.
- No need to rely on the strength of the installer.
- SAFE pre-engineered swage tool assures repeatable, leak-free and reliable connections.
- SAFE for maintenance repairs in hazardous areas.
- Can be installed on a wider range of pipe/tube wall thicknesses.
- SAFE for high pressure applications.
- Easy to install in tight tube runs side-by-side.
- Through bore design allows for zero clearance installation.
- No other sealants or lubricants required.
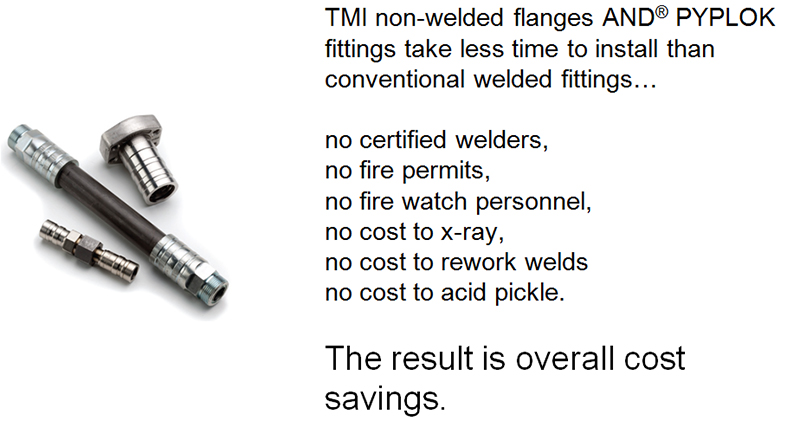
CNG – Compressed Natural Gas | Hydraulic Oil |
Paint and Sealer Lines | Low Temperature Steam |
Condensate Piping | LPG – Liquefied Petroleum Gas |
Deluge Systems | Lubrication and Grease |
Down Well Coiled Tubing | Natural Gas |
Drains and Plumbing Vents | Waste Water |
Ethylene Glycol/Water | RAD Waste Systems |
Fuel Oil and Fuel Gas | Solvents and Water Based Paints |
Gases – Nitrogen, Air, Helium | Subsea Piping |
Heating Coil | Steam Tracer Lines |
High Pressure Water Mist/Fog – Fire Suppression Systems |
Plant Instrumentation and Utility Air |
Benefits of a TMI non-welded system versus welded system
- No special skilled labour required vs. qualified welder.
- Actual flaring time is measured in “seconds” vs. “hours” for a welded joint.
- No special hot work permits
- No fire watch personnel required.
- No leaks as a result of stress fatigue cracks as seen in welds.
- No cost to x-ray welds.
- No cost to rework welds.
- No acid flush chemicals and neutralizers required.
- No added cost or environmental issues to dispose of chemical wastes.
- SAFE cold work technology.
- Tube-Mac Project Coordinators develop and cost up BOM.
- Field bend and fabrication – reduces engineering design time.
- On-site container – reduces warehouse and inventory costs.
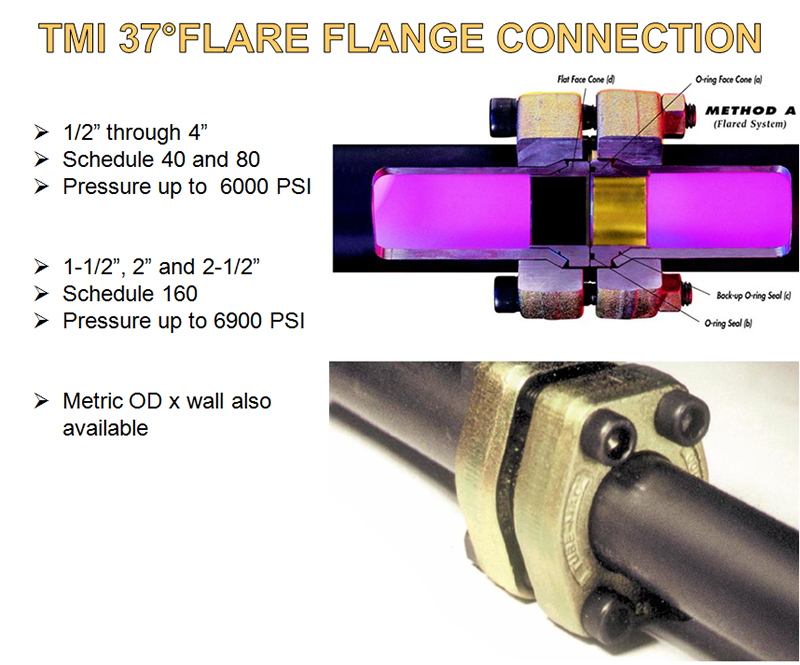
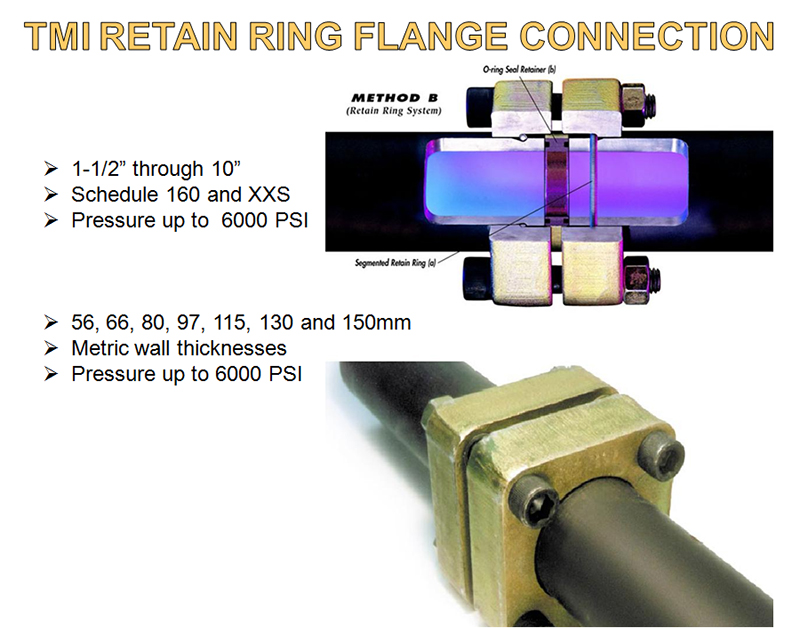
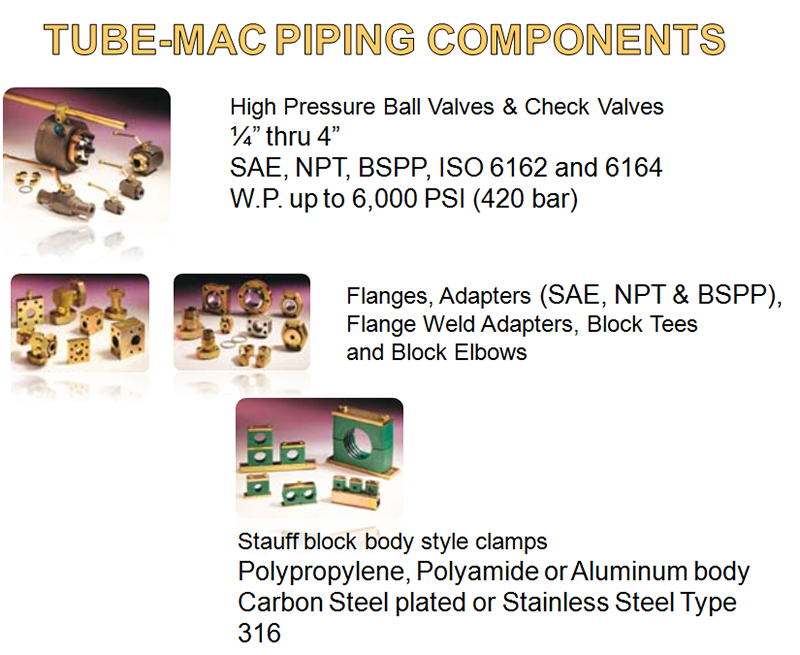
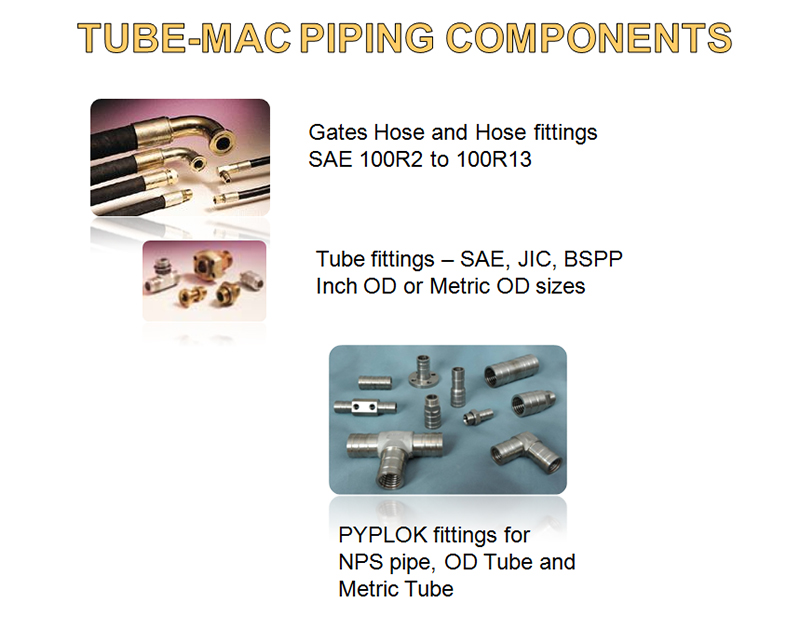