![]() |
![]() |
Step 1 : Root Blower Intermediate Side Plate | Step 2: Crack in Between Rotor Seating Areas, Approx. Length 60mm x Thickness 12.5mm |
![]() |
![]() |
Step 3 : To Install First Stitching Pin AtThe Edge | Step 4 : To Carry Out Installation of Subsequent Pins |
![]() |
![]() |
Step 5 : Pins Installed In Overlapping Pattern | Step 6 : To Grind Flat Protruding Pin Heads |
![]() |
|
Step 7 : Grind Smooth Entire Surface. Job Completed! |
Metal stitching is a crack repair process in cast metal without welding. The cracked metal is replaced by metal stitching pins that installed by drilling and tapping to draw the side of the crack together. The stitching pins with its special thread design creates a radial drawing pressure and pull the surrounding materials of the crack together, and permanently seals and lock it together.
Why Metal Stitching?
- The need for an alternative to difficulties encountered in welding. Electric welding for cast iron is less than satisfactory and in many cases can create even more cracks.
- Metal stitching is a cold repair process which will not create distortion or further damage to the parent material.
- If failed weld attempts damaged the metal, metal stitching repair may be possible after the affected area has been cut out so that new patch can be stitched in.
- Restore broken parts to original strength
- On-site repair is available with little or no disassembly.
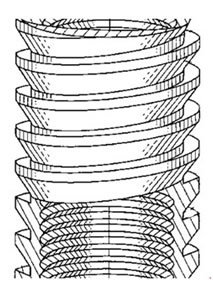
Stitching Pin with Spiral Hook Thread Design

Installation of stitching pins creates radial drawing forces that pull sides of crack together
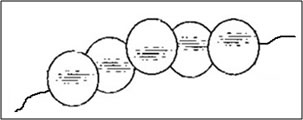
Pins are installed in an overlapping series to “stitch” the crack line